CONDUCTIVE FILAMENTS DEVELOPED FOR FDM PRINTING OF RESISTIVE SENSORS
For the successful embedding of sensors into composite products, it is required to develop thin and flexible sensors on materials, which are ideally made of a similar raw material as the final product. Thin and porous cellulosic papers are very suitable sensor substrates and used within the i³ Sense program as sensor carrier material. In addition to screen printing and physical vapor deposition, new methods have been developed in i³ Sense for establishing conductive sensor structures on paper or wooden surfaces.
Meanwhile, digitally linkable printing technologies, which allow freedom in the geometrical design of an electrode structure, are increasing their market share within industries such as aerospace, automotive, healthcare, and consumer goods. Potential use cases include quality monitoring, in-situ process monitoring, smart house concepts and flexible paper electronics.
Wood K plus successfully prepared a 3D printed sensor on cellulosic paper, via the fused deposition modeling (FDM) process (Figure 1) and laminated them on a fiber board (Figure 2). This development included the preparation of conductive thermoplastic compounds with commercial carbon fillers, filament extrusion, 3D printing of a resistive sensor, lamination into a composite and sensor validation during several loading cycles (Figure 3). For this approach, the development of premium filaments was required, tailored to meet the specifications in flexibility, conductivity, processability and long-term stability.
Especially, for the development of electrically conductive thermoplastics with sufficient chemical stability against epoxy resins, several changes in the material selection were necessary, so that the final formulation could withstand harsh processing conditions during a lamination process.
Wood K plus’s many years of experience in producing thermoplastic compounds for the extrusion of easily printable filaments was crucial for the development of a stable sensor structure on paper.

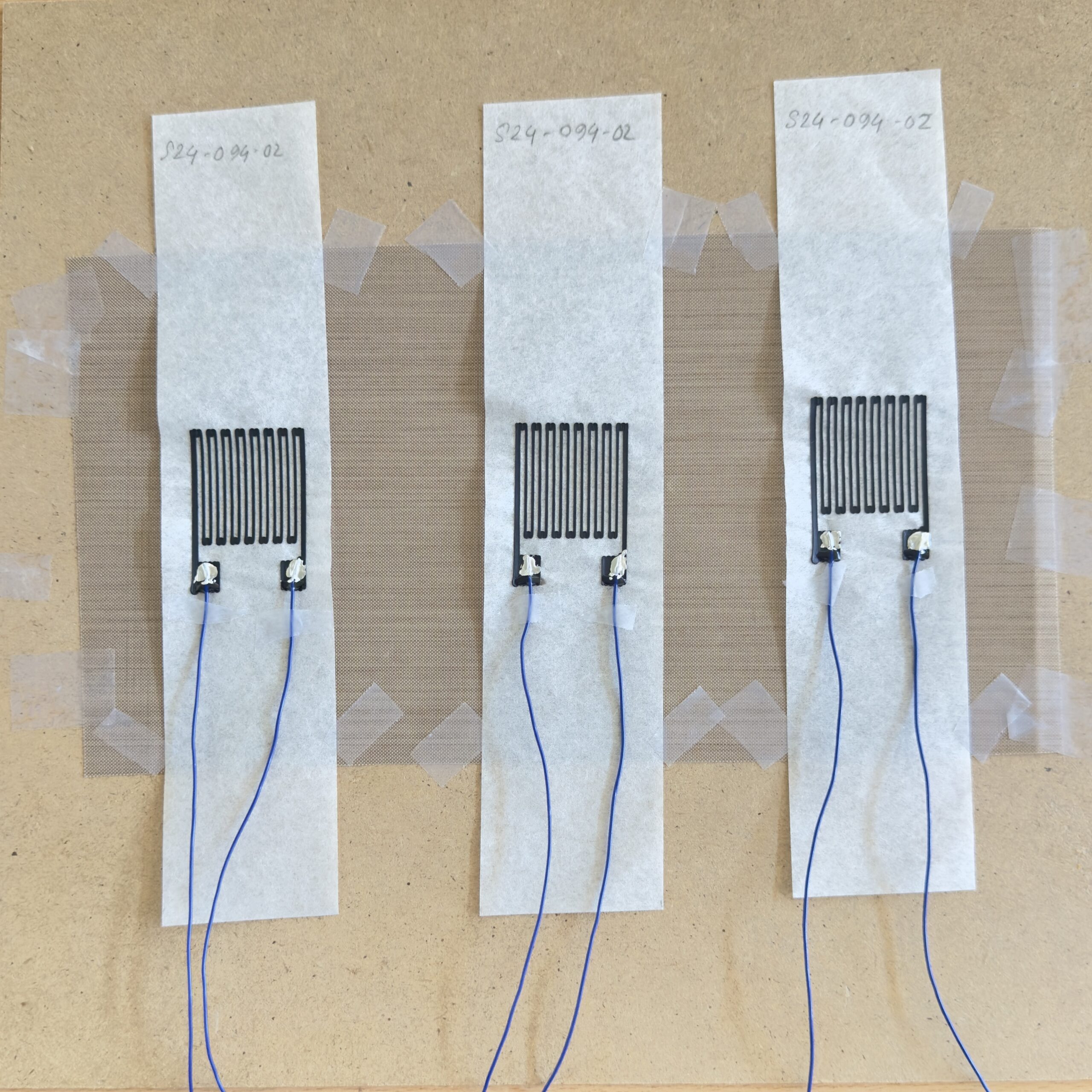
Figure 1: Prepared conductive filaments and 3D FDM printed conductive structures on thin cellulosic papers ©Wood K plus
Impact and effects
New fabrication techniques enable conductive structures on biodegradable sensor substrates. 3D FDM printing with biodegradable materials allows the creation of strain sensors, combining functional materials with advanced processing. These sensors support structural health monitoring, ensuring composite durability and safety.
Project partner
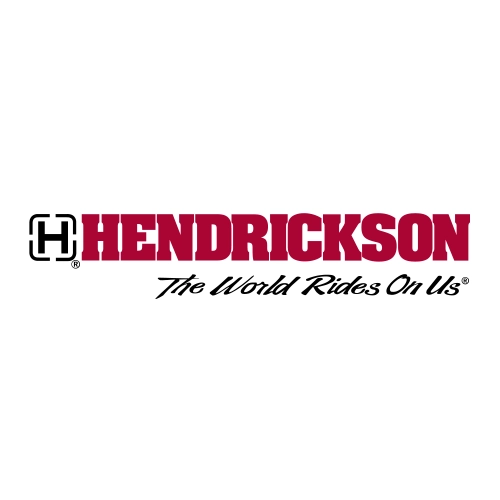
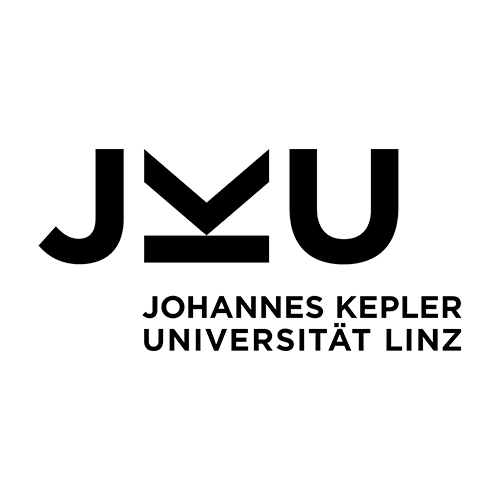
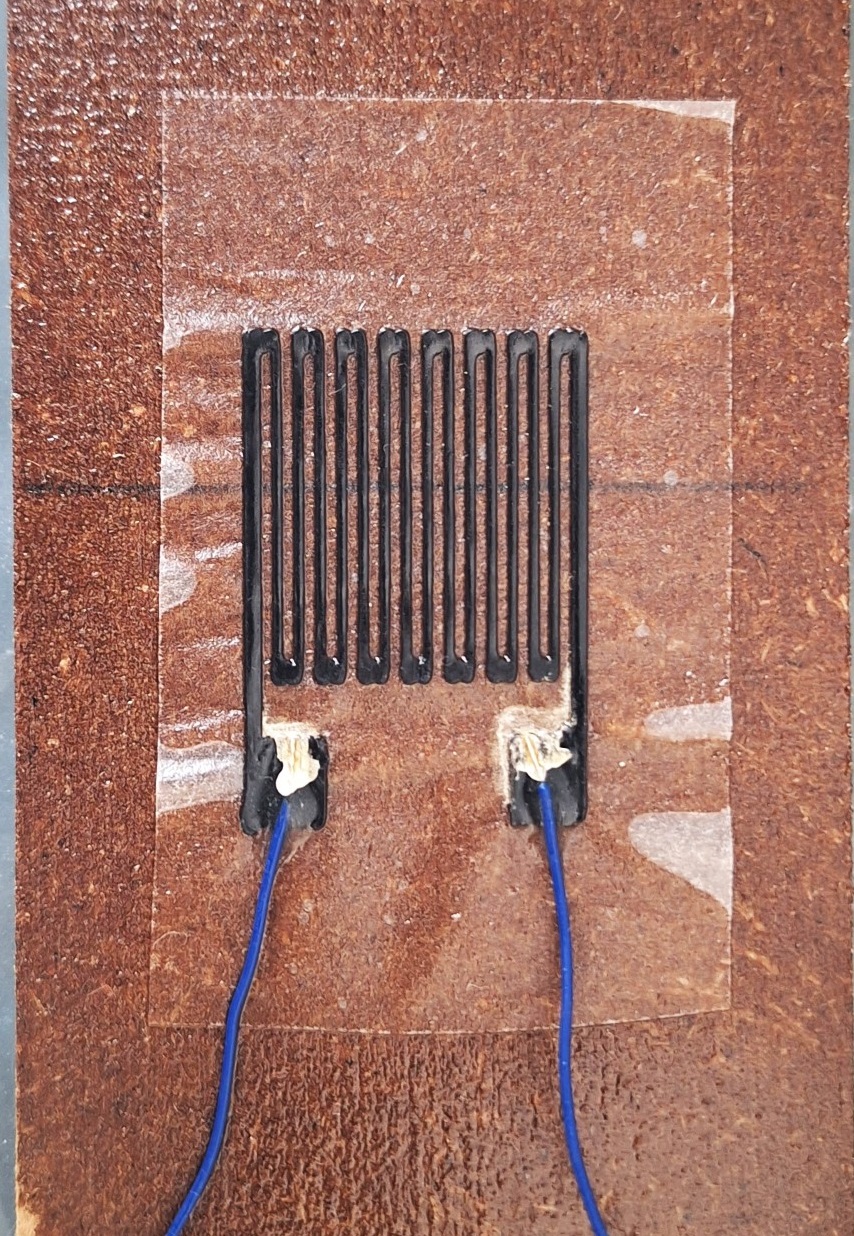
Figure 2: 3D printed paper-based sensor samples laminated on a fiberboard © Wood K plus
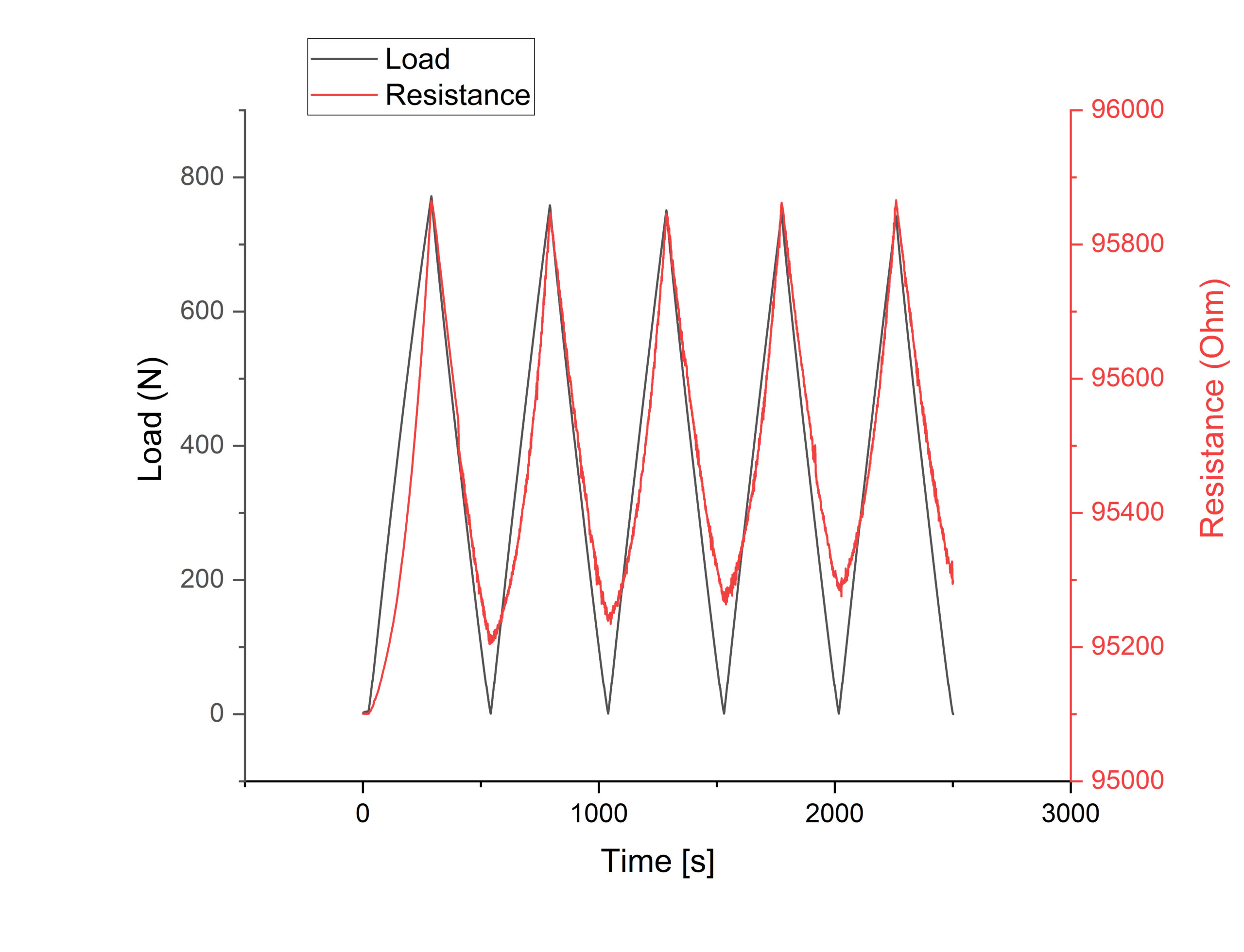
Figure 3: 3D printed paper-based sensor sample, tested
after lamination on a fiberboard: 5 cycles, flexural test,
material: PA12-MWCNT filled © Wood K plus
More details
Lead Partner:
Wood K plus - Kompetenzzentrum Holz GmbH
Project Management:
Claudia Pretschuh, PHD
Project partners:
Hendrickson Austria GmbH, JKU Linz, SoMaP
Funding Programme / Project ID:
FFG, KWF, Land NÖ, Land OÖ, BMK, BMAW
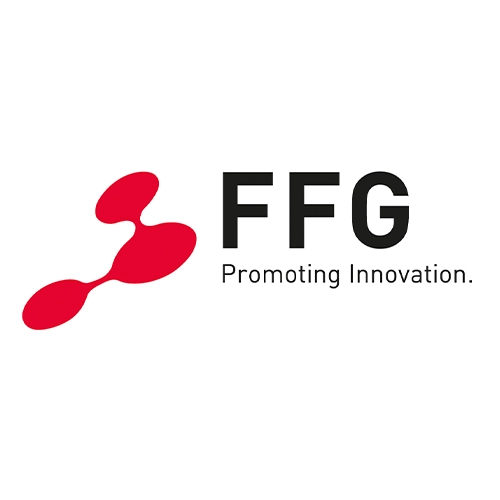
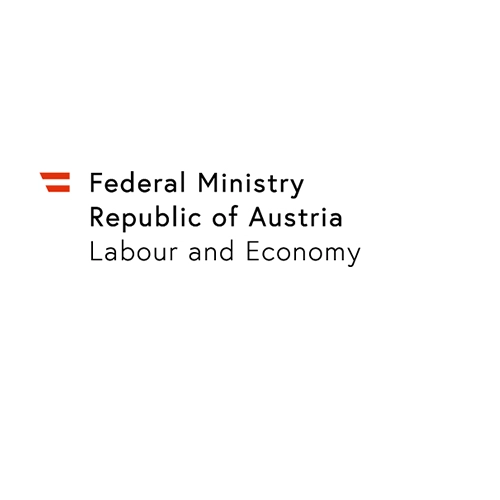
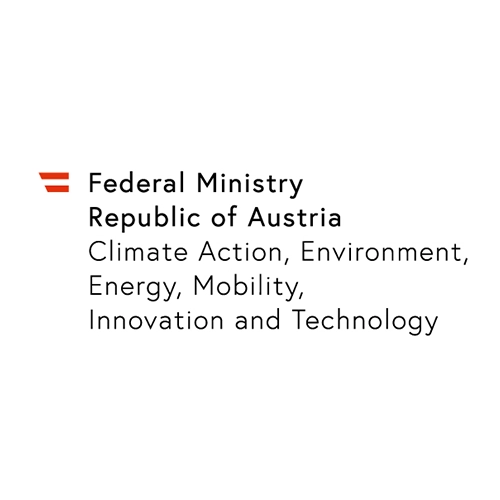
This success story was provided by the center management and by the mentioned project partners for the purpose of being published on the FFG website. Wood K plus is a COMET Center within the COMET –Competence Center for Excellent Technologies Programme and funded by BMK, BMAW and the provinces of Carinthia, Lower Austria and Upper Austria. The COMET Programme is managed by FFG. Further information on COMET: www.ffg.at/comet